Sand Casting
1: Sand Casting Construction and Methods
Sand casting is thousands of years old, having been first introduced in 1000 BCE. Over the centuries since, it has had improvements in process controls, material options, tolerance capabilities, the intricacies of parts, and the range of part sizes but with slight changes in the types of metals used. The results of engineering, innovation, and development has made sand casting the most versatile and widely used metal casting method.
What is Sand Casting?
Sand casting is a manufacturing process in which molten metal is poured into a sand mold containing a hollow cavity of the desired shape. After a period of time, the casting cools and solidifies. The sand is then broken away and shaken out. Casting materials for sand casting include metal, concrete, epoxy, plaster, and clay.
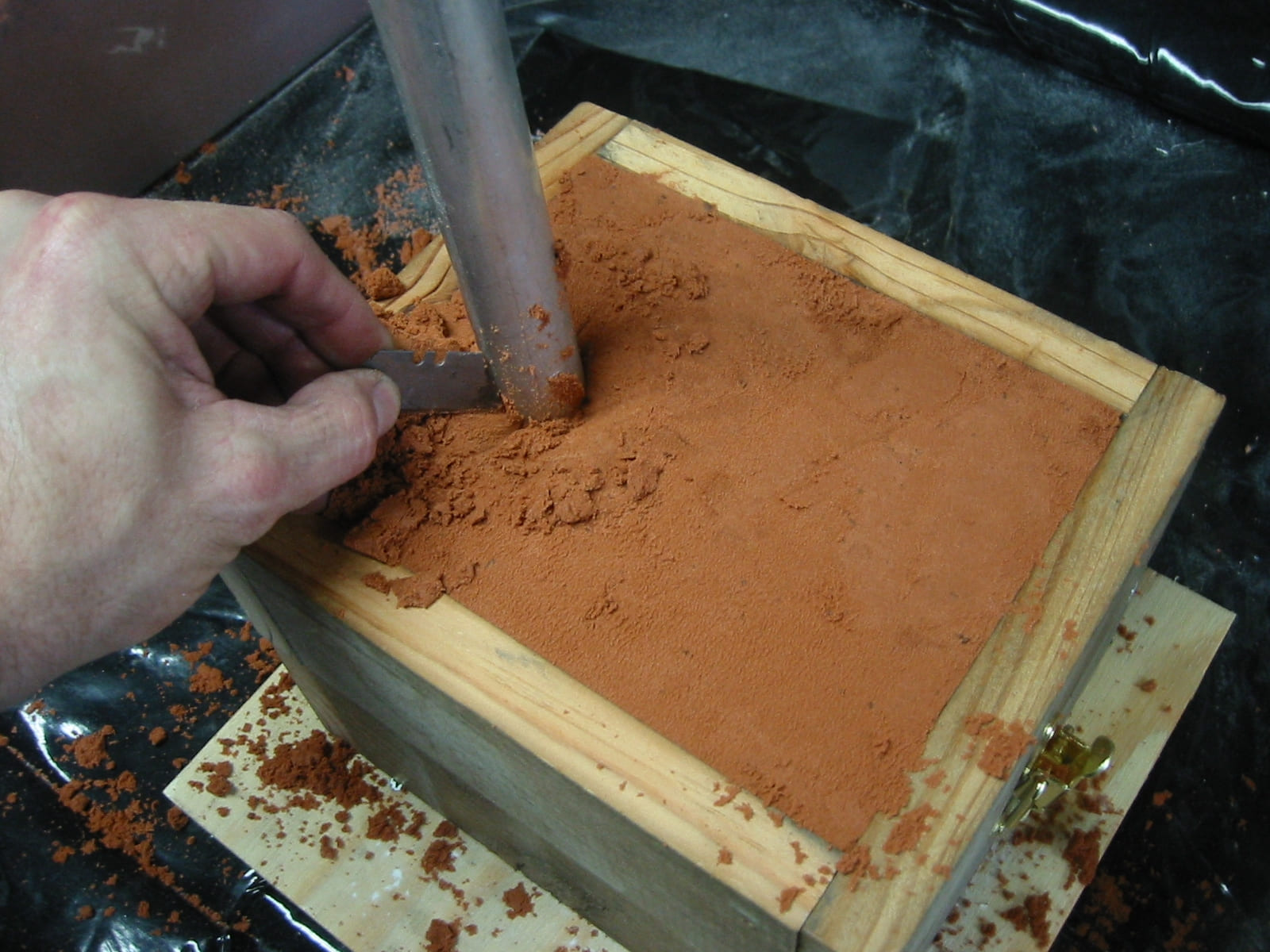
Casting is a manufacturing process in which a liquid material is usually poured into a mold, which contains a hollow cavity of the desired shape, and then allowed to solidify. Casting materials include metal, concrete, epoxy, plaster, and clay. This article will focus on sand casting.
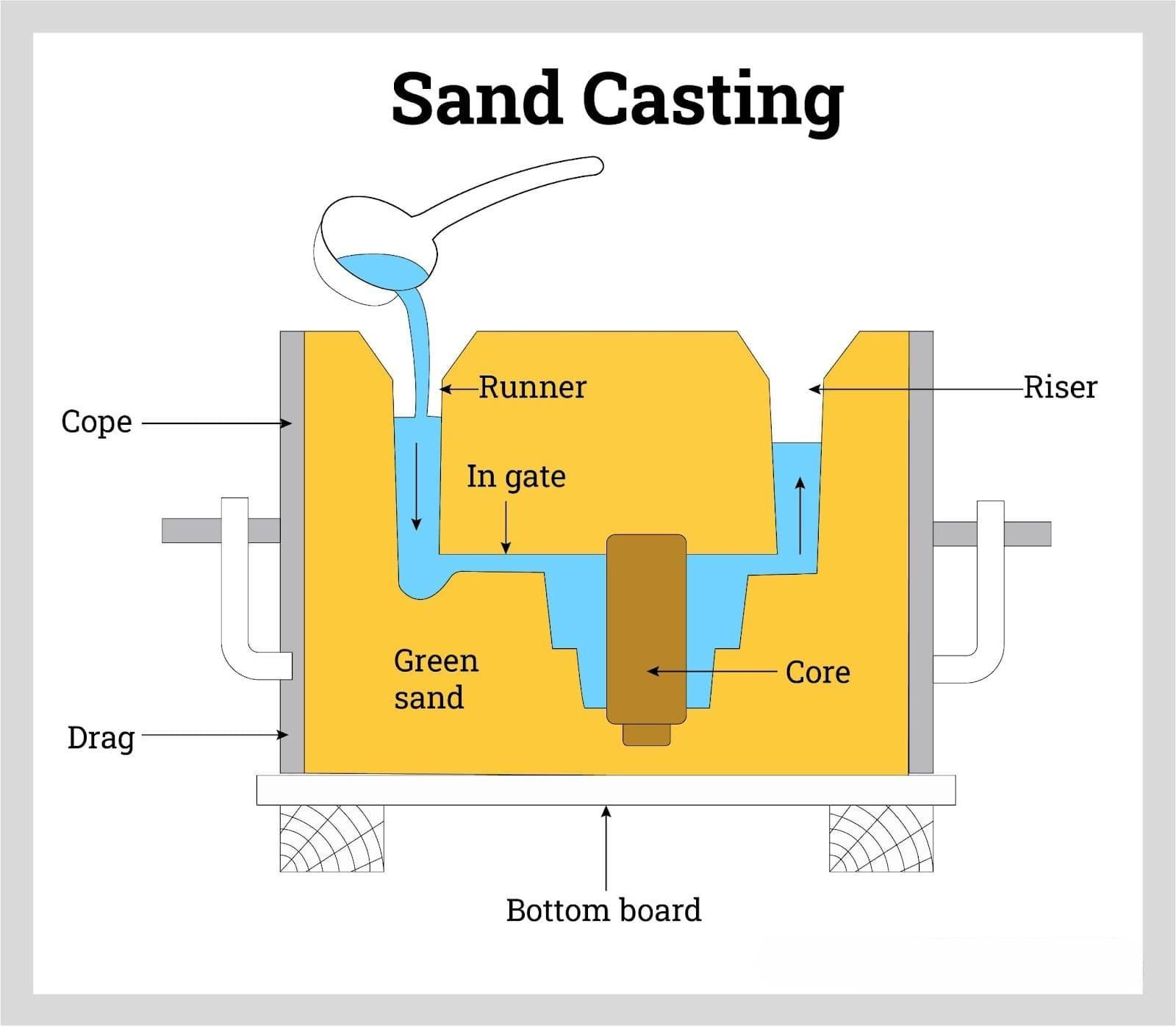
Parts manufactured using sand casting come in a wide range of sizes and weights and have complex geometries using a variety of metals. The use of sand as the casting material significantly reduces the cost of the casting process. In the metal mold process, the machining of the molds accounts for a large portion of the costs.
With sand casting, the type of sand used in the process depends on whether the sand will be reused or disposed of. In green sand sand casting, the molds are reusable while in the dry sand casting process, the sand is thrown away.
Sand casting is used for metals with high melting temperatures, such as titanium, steels, and nickel and is the only casting process that can work with those materials. It is the choice of the aerospace and automotive industries for producing low cost, small series parts.
Components of a Sand Casting Mold
The making of the sand casting mold usually requires four components which are:
Base Sand
The base sand is the sand that is utilized to create the mold in its purest form. A binding agent is necessary to keep it together. The core is also made of base sand. The following are the most prevalent varieties of base sand:
Silica sand
Olivine sand
Chromite sand
Zircon sand
Chamotte sand
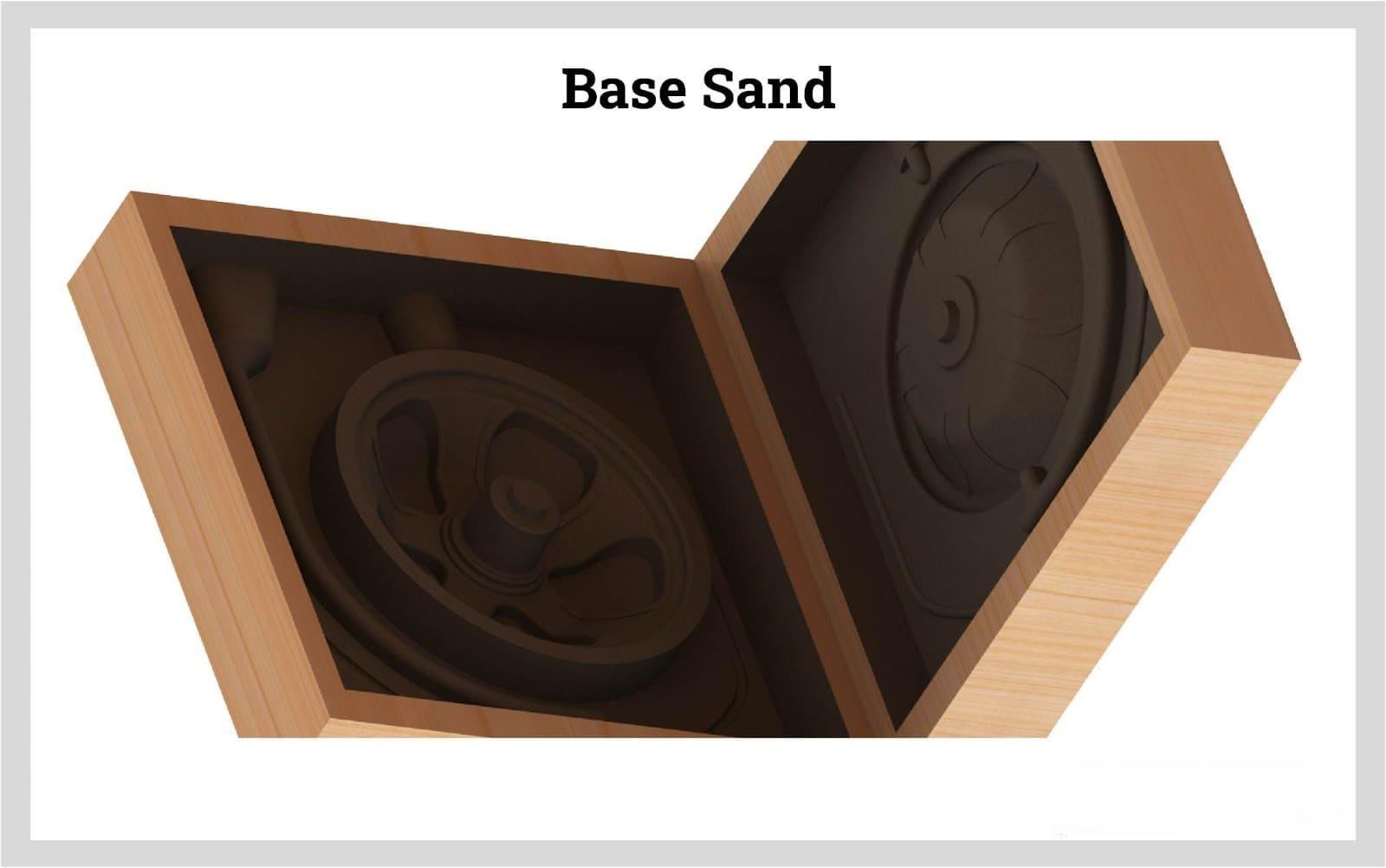
Binders or Binding Agents
The binding agents are the glue that holds the sand particles together. The following are the most frequent types of binders:
Clay and water
Oil
Resin
Sodium silicate
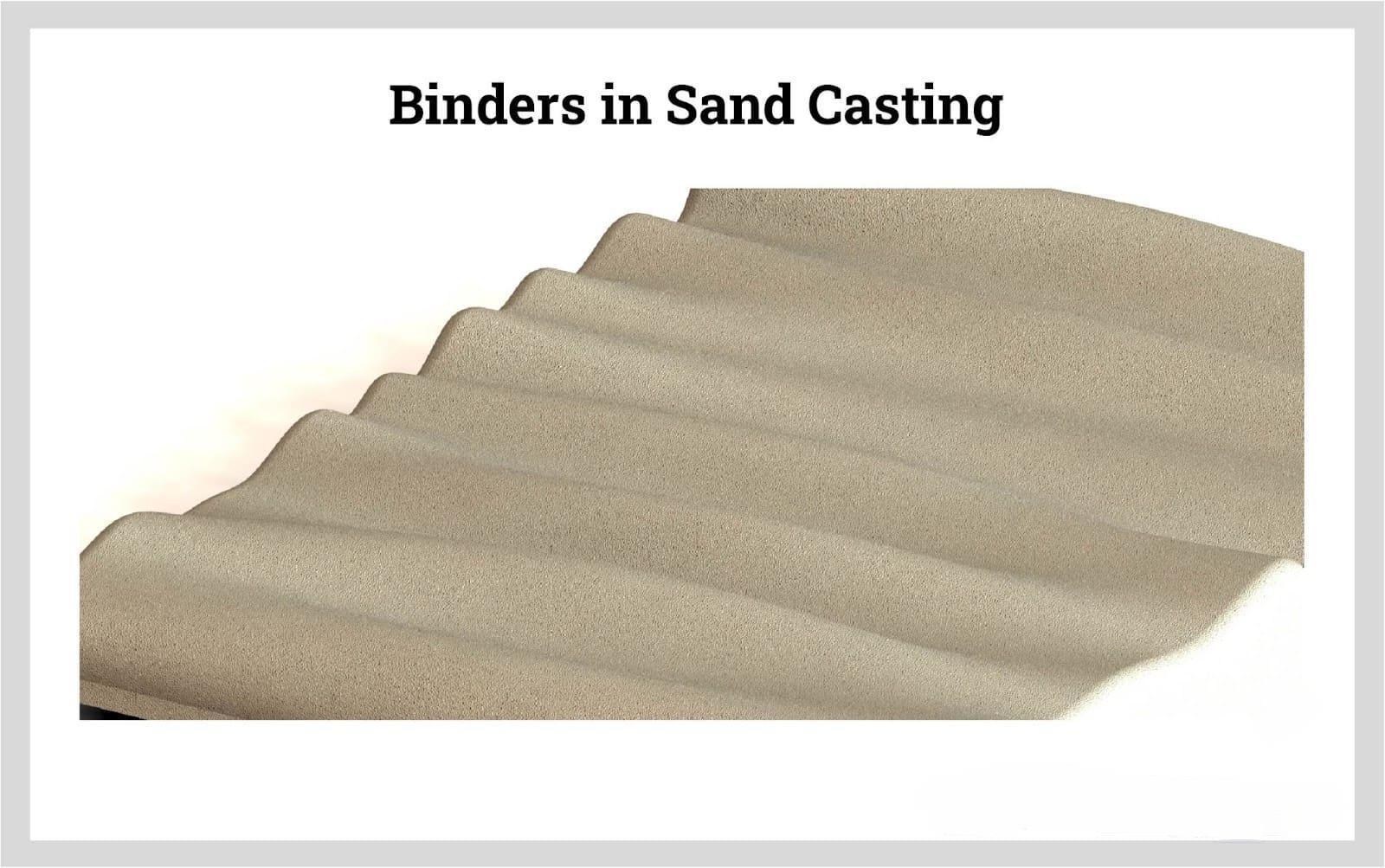
Improvement Through Additives
Additives are used to improve the mold surface finish, its strength, refractoriness, and cushioning.
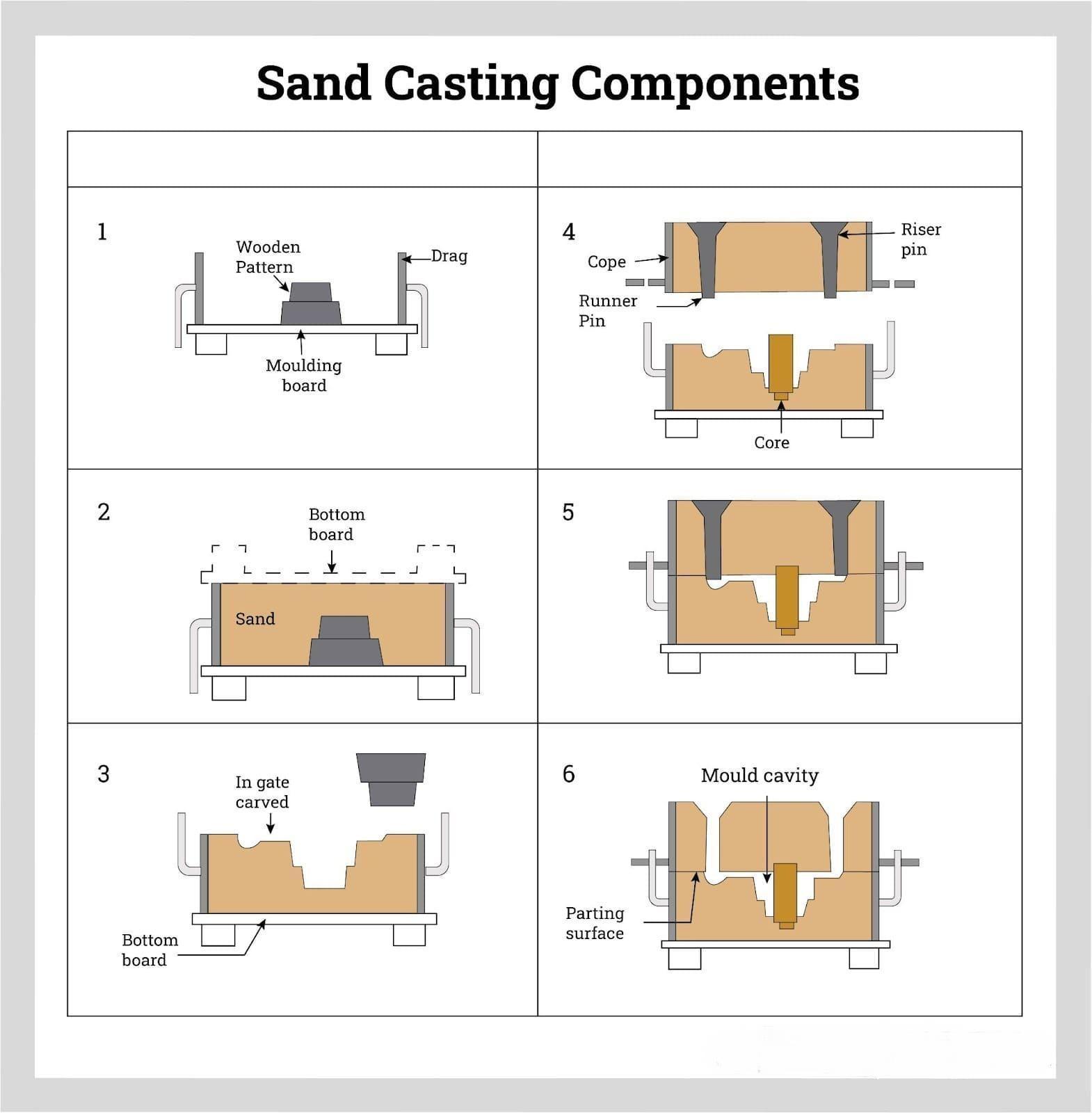
Parting Compounds
This can be a fine powder or liquid used to facilitate pattern removal from the mold.
Sand Casting Methods
Sand casting is a centuries old manufacturing process that developed in China around 1600 BCE. At the time, it was used to produce statues, decorative ornaments, and artifacts. With the introduction of airplanes and automobiles in the 20th century, sand casting became an essential part for producing highly accurate parts with exceptional tolerances. Since then, ancient sand casting has been improved, adjusted, changed, and engineered to be a vital part of 21st century parts and components production.
It is estimated that 70% of metal castings in the world are completed using sand casting. It is an essential production method for the manufacturing of engine blocks, cylinder heads, pump housings, valve bodies, and gearboxes.
Bedding-In Sand Casting
The 'bedding-in approach' can also be used to form the solid cylindrical design. The drag is partially filled with molding sand and rammed in this technique. The pattern is driven into the sand after enough pounding. To ensure accurate sand ramming, the sand near the pattern is tucked and slammed tightly.
The pattern may be removed for the sand to be examined for soft patches on the surface. If there are any soft patches, ramming with more sand is done until the sand is tightly packed. To ensure a well rammed mold chamber, the pattern is forced downward, again.
The dividing line should be level with the surrounding smooth sand surface when bedding-in. The drag does not need to be rolled over when a pattern is bedded in. When employing pit molding to make larger molds, bedding-in can be used.
False Cope Sand Casting
Another method for molding the solid cylindrical design is the false cope technique. In this process, the sand is rammed tightly beneath the pattern. The design is bedded into the coping without regard for sand ramming beneath the pattern, resulting in a smooth parting surface.
After dusting the cope and pattern with separating sand, the drag section of the flask is placed on top of the cope and is followed by the standard ramming procedure. The completed assembly is gripped and rolled over on a sand bed and the clamps, cope, and cope bottom board are removed and destroyed. The empty cope is placed on the drag and rammed. In this case, the cope is a dummy block that is used to create the drag and is referred to as a 'false cope.'
Flat Back Sand Casting
With flat back sand casting, the mold cavity is on the drag side, the cope side, or both. With an unmolded cope, a sprue is placed in the drag to form the flat back to help with the pouring and cooling of the molded part. The pattern is placed into the drag box, covered in sand, and rammed. This is used for simple flat back parts or for a flat back part that will be joined to its other half in the joining of the cope and drag.
With simple flat back parts, the rammed pattern is removed and gates and sprues are inserted to allow molten metal to be poured into the mold. When flat back sand casting has the pattern in the cope and drag box, the cope is placed over the drag box and an identical or similar pattern is placed over it and rammed such that the two patterns make a firm complete impression.
The cope and drag box are separated and the patterns are removed after which the cope and drag box are placed back together and tightly sealed to keep the upper box from floating. Gates and sprues are added for the pouring of the molten metal. Once the metal has cooled and solidified, the part is removed and finished.
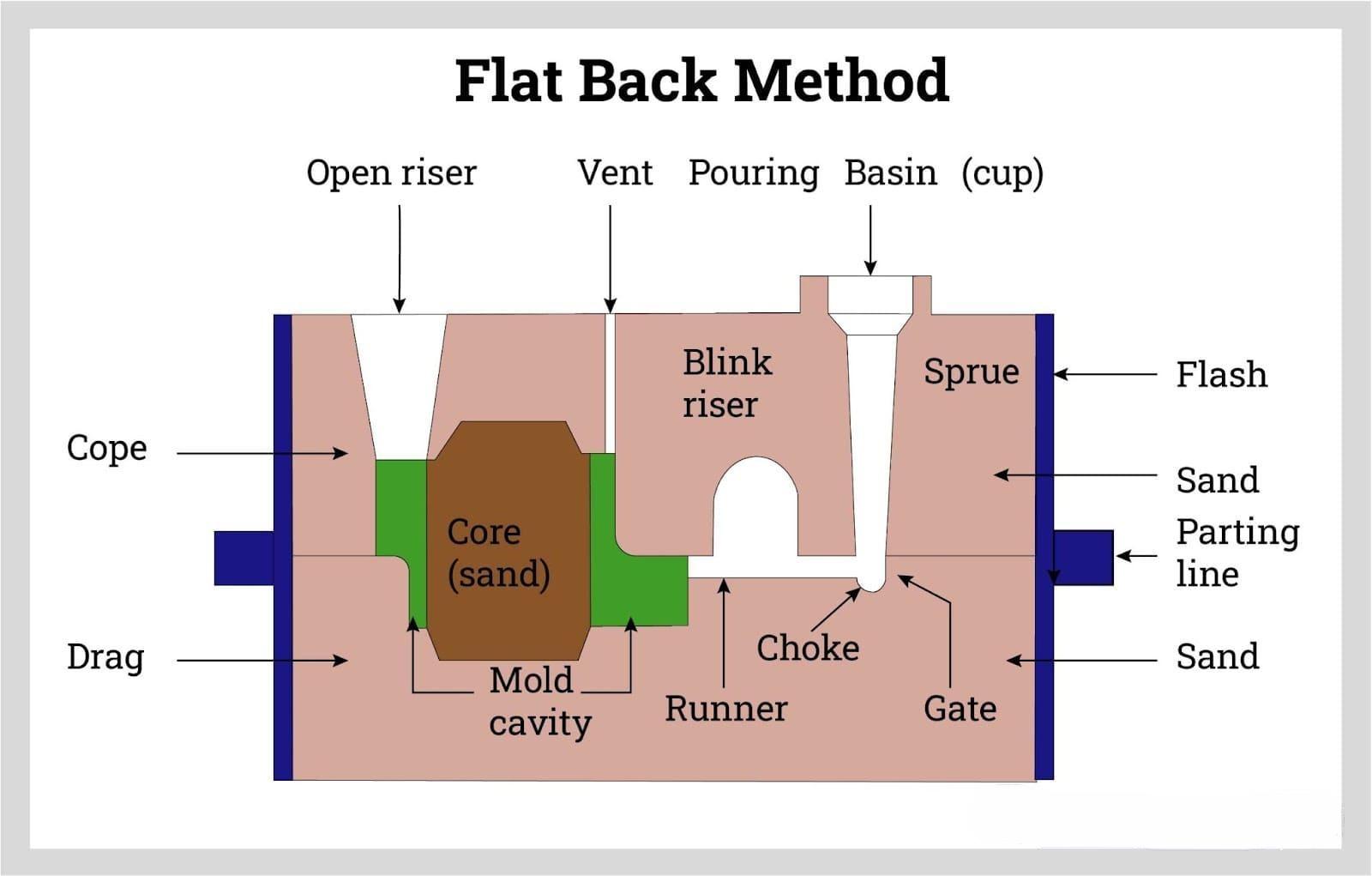
Skin Dried Sand Casting
In skin dred sand casting, a thin layer of sand is placed over the mold cavity and dried by a heater, torch, heat lamp, or the ambient air. The dried skin layer provides an exceptionally smooth surface finish and is made up of fine grain sand mixed with a binder. Molten metal is poured into the mold cavity filling the space between the pattern and the skin sand layer.
As with all forms of sand casting, the sand is removed when the part cools and solidifies. The skin dried process is ideal for parts that require an extremely smooth and uniform surface, such as engine, aerospace, and machinery parts.
Water Glass or Sodium Silicate Sand Casting
Sodium silicate sand casting is a form of green sand casting where sodium silicate is used as the binder. The use of sodium silicate allows for rapid production of the casting mold and involves curing the sand and sodium silicate with carbon dioxide (CO2), which instantly hardens the mold. Prior to the hardening process, other materials, such as resin, oil, cellulose, or polysaccharide, are mixed with the sodium silicate such that it will break down when removing the casting.
Sand is mixed with a sodium silicate solution and packed around the pattern for the casting. CO2 quickly cures and hardens the mold. Once the mold is solidified, the pattern is removed from the hardened mold and molten metal is poured in. The cooled and solidified part is broken from the mold and the materials are disposed of.
Water glass sand casting is used for the manufacture of complex and intricate parts since the sand is capable of creating complicated shapes and patterns. It is an inexpensive process that involves little machinery but produces castings with rough uneven surfaces that require finishing.
Vacuum Sand Casting
Vacuum sand casting, known as the V-process, uses a thin sheet of plastic that is draped over the pattern that has been vented such that a vacuum can be pulled through it. A vacuum flask is placed over the plastic covered pattern and is filled with sand, which is vibrated to compact it. A sprue and pour cup are placed in the cope. A second sheet of plastic is placed over the sand, and a vacuum is drawn through the sand and plastic sheets that hardens and strengthens the sand.
The process is repeated for the formation of the drag. The molten metal is poured while the cope and drag are under the vacuum. During the process, the plastic vaporizes as the vacuum maintains the shape in the sand as the molten metal slowly solidifies. Once the part is cooled and set, the vacuum is removed.
Vacuum sand casting is known for tolerances of ± 0.01 in and ± 0.002 in with cross sections as thin as 0.090 in (2.3 mm). Surface finishes are excellent without moisture defects, the cost of a binder, and no toxic fumes.
Shell Sand Casting
Shell sand casting uses a resin coated sand to form a shell like mold, which is heated until it hardens. After the formation process, the shell is assembled and molten metal is poured into it and allowed to cool. Once the metal has cooled, the shell is broken and the part is removed.
The process for shell sand casting or molding is more expensive than traditional sand casting, which makes the cost of parts higher. Shell sand casting requires fewer steps, creates far less waste, and is cost effective for its accuracy and efficiency. Additionally, shell molding can produce parts at a faster rate in large quantities.
The main distinguishing feature of shell sand casting is its resin coated molds, which make shell sanding casting more precise and accurate than traditional sand casting. In a single step, intricate, complex, and detailed components are quickly manufactured with smooth even surfaces with exceptionally accurate dimensions and tolerances that removes the need for secondary finishing.
How Sand Casting is Done
When sand casting, several steps are followed which include:
Producing the Pattern – Desired Product
A reusable pattern with the same details as the desired completed product is used in the process. A pattern is always made larger than the final part to give an allowance for thermal contraction or shrink. Shrinkage allowance will account for the contractions that occur as a casting cools to room temperature.
Liquid shrinkage is a reduction in volume that occurs when a metal transitions from a liquid to a solid form. To compensate for this, the mold has a riser that feeds liquid metal to the casting. Solid Shrinkage: When a metal loses its solid state temperature, it shrinks in volume. To account for this, shrinkage allowance is included in the patterns.
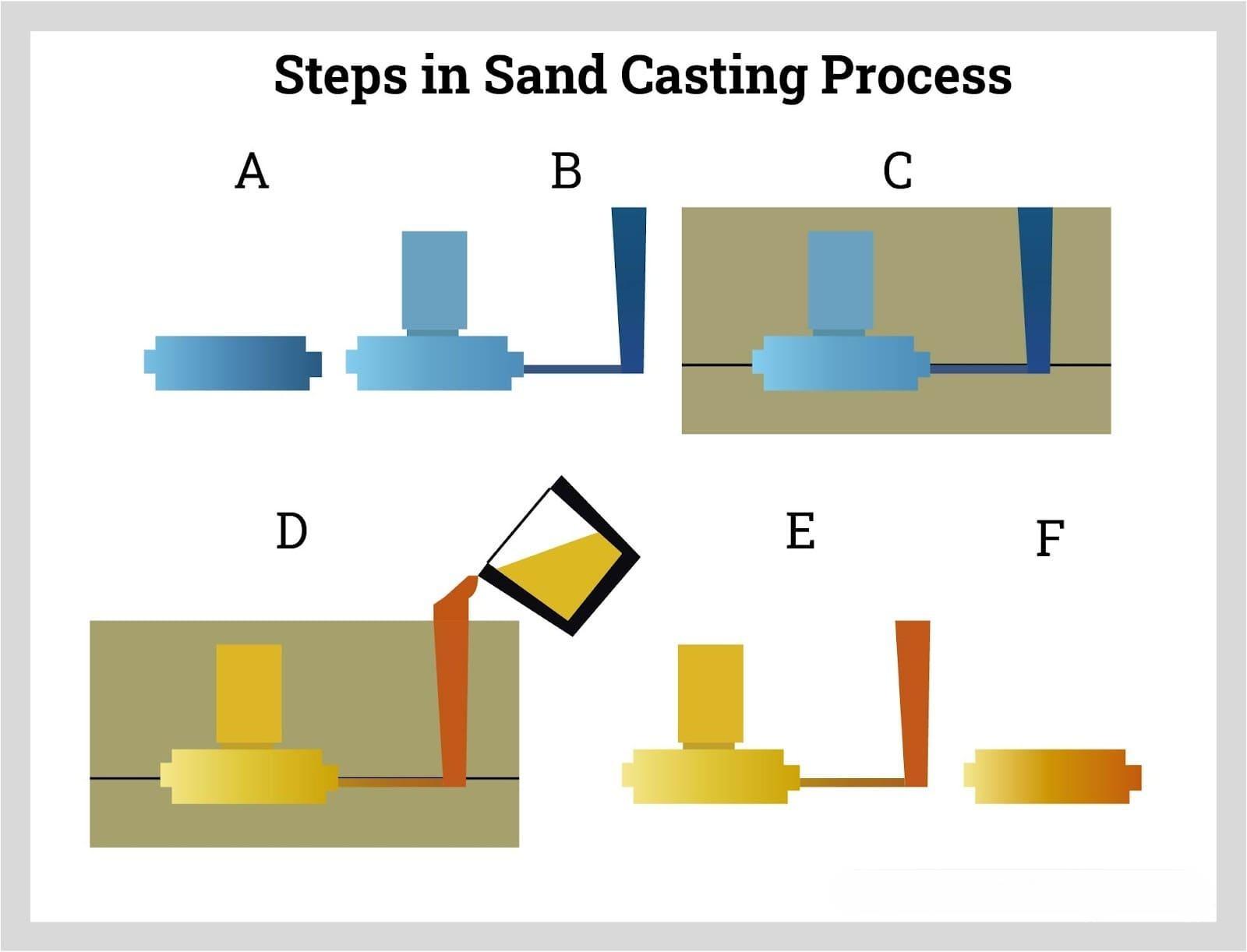
The machining allowance will cover the extra material that will be eliminated in order to produce a completed product. The rough surface of the cast product will be eliminated in this process. The size, material properties, distortion, finishing accuracy, and machining method all influence the machining allowance. To ensure that the pattern is removed safely, all surfaces parallel to the pattern removal direction are tapered slightly inward. This is known as draft allowance.
Pattern Creation – Gates and Risers: Metal Delivery System
The metal channels that will feed the required cast product design with proper gating and risers are also included in the pattern. This regulates the metal flow and requires gas venting while driving the unavoidable thermal contraction to acceptable places (other than the actual desired finished product).
Depending on the volume and tolerance required, patterns are manufactured of a variety of materials, including wood, metal, synthetics, expandable polystyrene (EPS), and others. In other circumstances, such as pipe fittings, the component’s interior must be hollow. In such circumstances, extra patterns known as cores must be created.
Core Making
Cores are a separate portion of the mold that prevents the liquified material from filling in any gaps. They're utilized to make interior cavities and other things that the mold can't produce. A core box is the tooling used to build the core, which is just another name for the mold that makes the core.
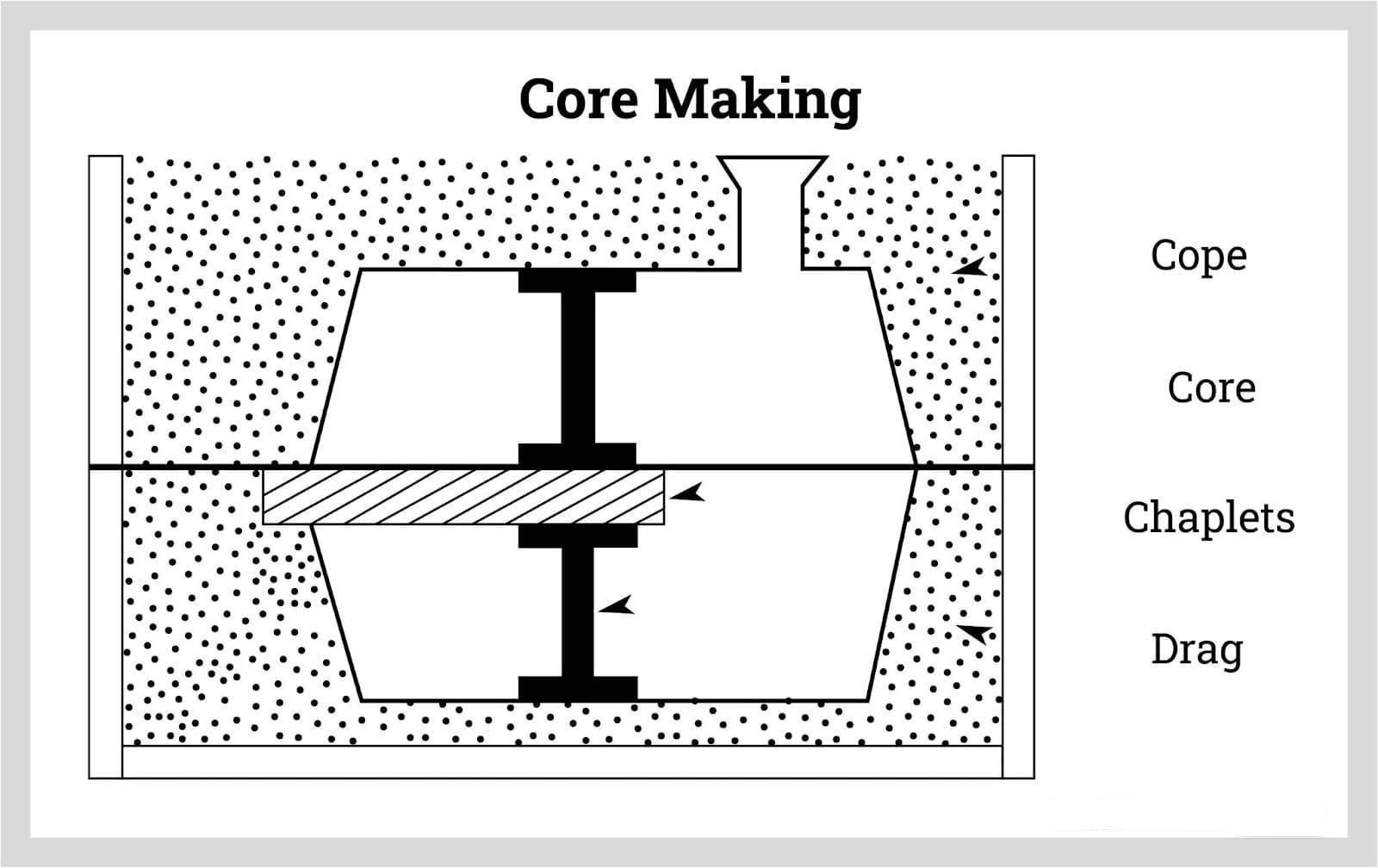
The materials used to make the core must meet certain criteria:
It must be strong enough to withstand the turbulence caused by the molten material
It must have a good hardness
It must have a high permeability so that the gasses formed during the casting process can easily escape
It must be able to withstand the high temperatures caused by the molten material
Smooth surface finish
Minimal gas formation when exposed to the molten material
It must be weak enough to break while the molten material cools and shrinks, allowing it to be removed after solidification.
Creating the Mold
Around the design, a refractory substance that is stable at high temperatures (in our case, sand) is created. The material must be strong enough to support the weight of the liquid metal during casting. It should also be resistant to metal reaction but fragile enough to be separated after cooling of the casting.
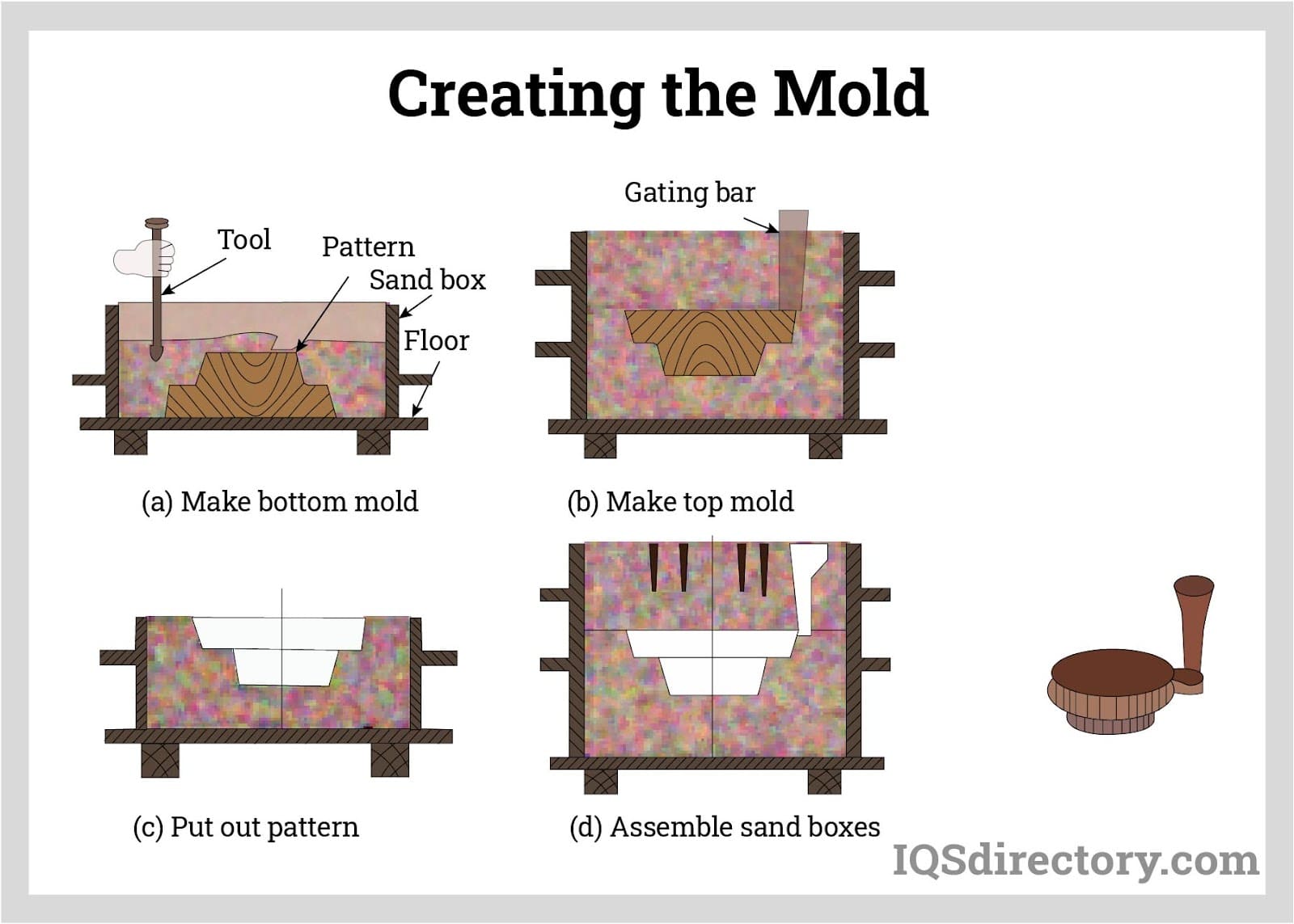
The mold can be made out of a variety of different sand materials. Other elements, such as clay or a chemical bonding agent, are usually added to the sand to make it stronger so that it can withstand the pouring operation. The mold can also be made by drilling the necessary shaped hollow straight into a block of sand. Because design changes may be handled and applied quickly, the technology is extensively employed during product development, or for portions with infrequent usage to avoid the storage or maintenance of a physical pattern.
The top half of the mold, known as the "cope," and the bottom half, known as the "drag," are usually made in two sections. The parts are split and the pattern removed once the sand has set (using the traditional/non-machined procedure). To improve the surface finish and protect the mold from the turbulence of the poured metal, a refractory coating is applied. The halves are reassembled, resulting in a cavity in the pattern's form. Cores, a means of producing appropriate internal pathways in the final product, may be included in the mold.
Pouring the Metal into the Mold
Molten metal is injected into the static mold directly. It defines the finished portion and the risers by filling the void. A continuous liquid metal supply comes from the risers to the casting. Because they are meant to cool and solidify last, the shrinkage and potential void are concentrated in the riser rather than the targeted section.
Liquid metal can thus flow into the casting smoothly with less turbulence. Reduced turbulence can aid in the prevention of oxide formation and casting flaws. This method can be used to make almost any alloy. Almost any alloy can be made using this method. For extremely reactive materials to oxygen, an argon shielding process can be used to keep air away from the molten metal.
Shakeout Operation
The casting hardens and cools, containing both the desired item and the additional metal required to manufacture it. In a shakeout operation, the sand is split up. The sand used to make the mold is recovered, reconditioned, and reused in large quantities.
Casting Final Operations
The gates, runners, and risers are cut from the casting, and final post-processing such as sandblasting, grinding, and other methods are used if necessary to finish the casting dimensionally. To achieve final dimensions or tolerances, sand castings may require extra machining.
Heat treatment can be used to improve the dimensional stability or characteristics of parts. Non-destructive testing is another option. Fluorescent penetrant, magnetic particle, radiographic, and other inspections are examples. Prior to shipment, final dimensional inspections, alloy test results, and NDT are validated.
2: Types of Casting Sand
Sand casting is a very versatile manufacturing method that provides developers, designers, and engineers with the freedom to create complex and intricate parts with high tolerances. It can be used with any form of metal, which is the reason it is the most common casting process.
Green Sand
Green sand casting is the most common form of sand casting. The sand used in green sand casting is not green but is referred to as green due to the presence of moisture in the sand, which is a mixture of sand, clay, water, and various additives. Molds used for green sand casting are reusable and are used to produce high volumes of parts. The sand cannot be reused and is disposed of after the casting process.
The sand for green sand casting contains 75% to 85% sand, 5% to 11% clay, 2% to 4% water, and 3% to 5% other materials such as silica. The clay and water act as binding agents and give the mold strength. Green sand casting does not produce parts with tight tolerances or precise dimensions. Parts created using green sand casting require secondary finishing.
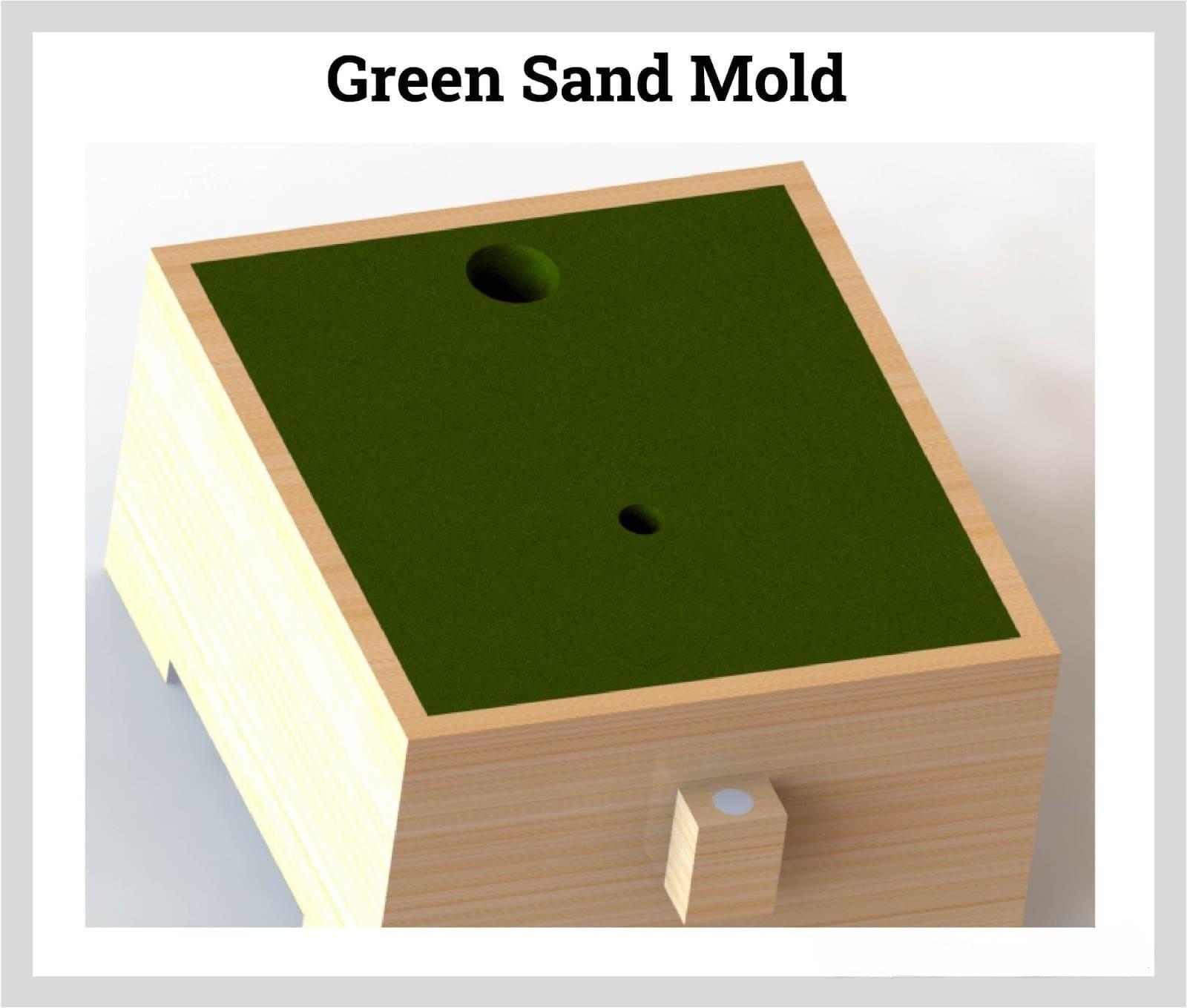
Dry Sand
With dry sand casting, sand is mixed with clay or other binding material, shaped in the form of the mold and baked to increase its strength. The baking process is the key to the casting process and has to be meticulously controlled to match the requirements of the binder. It is used for large ferrous and non-ferrous parts such as engine blocks, housings, gear boxes, and agricultural parts.
The popularity of dry sand casting is due to its ability to produce intricate designs with exceptionally close tolerances. As with green sand casting, cores and sprues are used to insert the molten metal into the mold. The complete process is complex, time consuming, and expensive but produces exceptional results. Unlike green sand casting, the sand from dry sand casting is disposed of at the end of the process and is no longer usable.
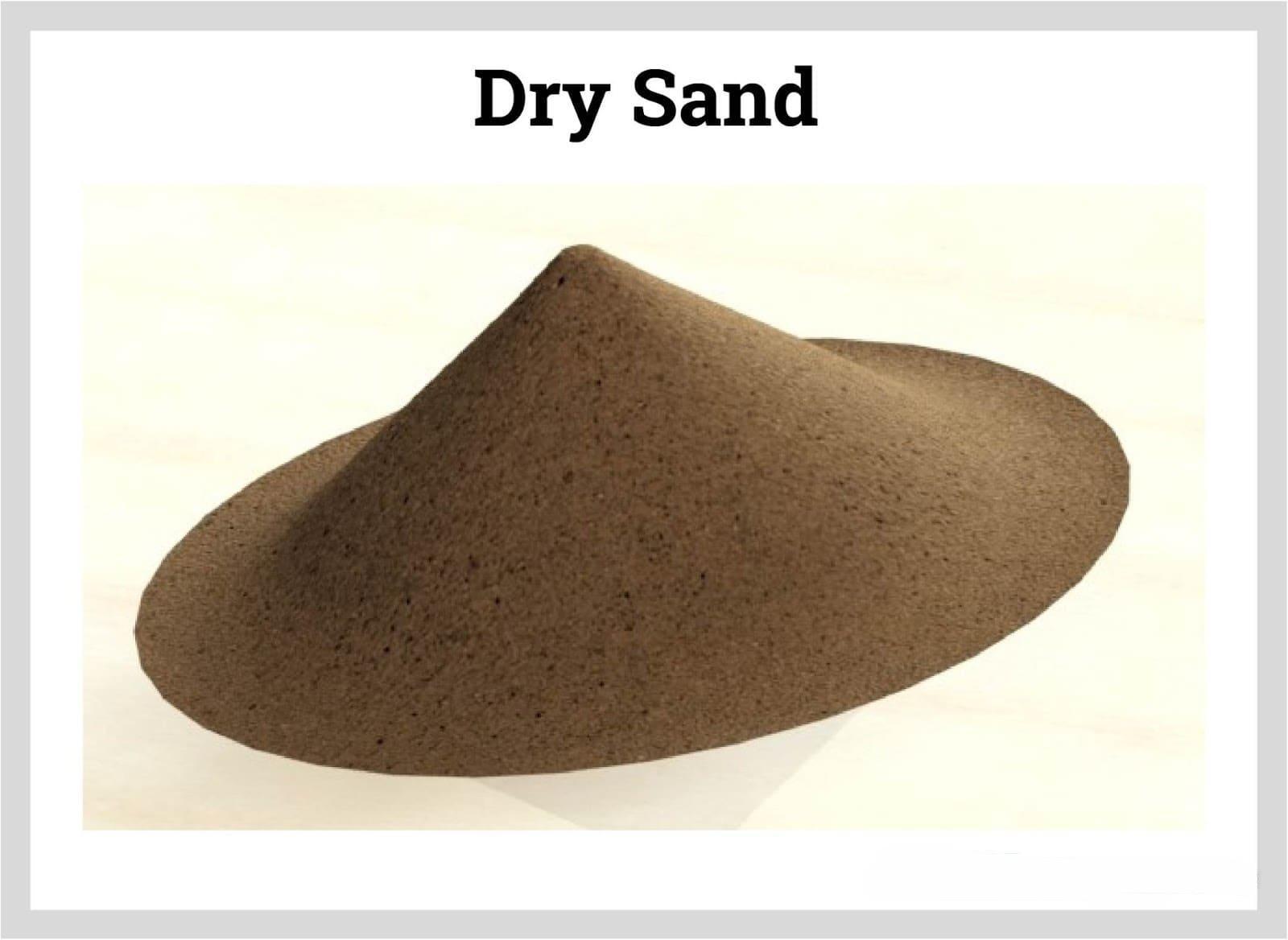
Facing Sand
Face sand is used to face the mold, as the name implies. Silica sand and clay are typically used to make face sand. That is, no sand from previous projects is used. It's placed just adjacent to the pattern's surface. Because it comes into direct touch with hot molten metal, facing casting sand must have high refractoriness and strength. Molding sand of this sort produces an extremely fine grain in the mold.
Core Sand
Silica sand is blended with core oil (linseed oil, resin, and mineral oil) and other binding elements including dextrin, cornflour, and sodium silicate in core molding sand. It is utilized to manufacture cores because of its great compressive strength.
Loam Sand
Loam sand is made up of an equal amount of sand and clay, and enough water. It's also utilized to make big, heavy things like hoppers and turbine parts.
Parting Sand
Pure silica sand is put on the faces of a design before molding with this sort of molding sand. Before the pattern is embedded in the molding sand, parting sand is sprinkled over it. This sand is also strewn across the contact surfaces of the cope, drag, and cheek.
Backing and Floor Sand
This casting sand, which is referred to as floor sand, fills the volume box and backs up the facing sand.
System Sand
This molding sand is suitable for large mechanical castings. It possesses a high degree of refractoriness, permeability, and strength. Machine molding is done with system sand to fill the flask completely. This molding does not utilize facing sand because it has been cleansed and has unique additives.
Molasses Sand
This molding sand has molasses as a binding agent and is typically used to make the core and sometimes intricate shape casting.
3: Sand Casting Metals
Sand casting is a highly adaptive process that can form any metal alloy including ones with high melting temperatures, such as steel, nickel, and titanium. The most common types of metals are aluminum, brass, cast iron, and cast steel. The choice of metal for casting determines the design functionality of the completed part and affects the casting’s quality, performance, and properties.
Production deadlines, quantities and volumes of parts, and different cooling and solidification rates also influence the choice of metal. The properties considered during the selection process are corrosion resistance, thermal conductivity, hardness, and how a metal adapts to temperature changes.
Non-Ferrous Metals
Aluminum
The term aluminum covers a wide range of alloys that are machinable and lightweight with strength that is similar to mild steel but less dense. Aluminum is commonly used for casting due to its castability, low density, and corrosion resistance. Base sands used for aluminum casting are silica, olivine, chromite, zircon, and chamotte that are combined with clay, oil, resin, and sodium silicate as binders.
Bronze
As with aluminum, bronze is a term used to describe several alloys of copper and tin that are altered by the percentage of copper, the percentage of tin, and the addition of other alloys such as aluminum, zinc, nickel, and iron. The three types of bronze used for sand casting are aluminum bronze, manganese bronze, and silicon bronze.
Aluminum Bronze consists of 9% to 12% aluminum and 4% to 6% iron and nickel with the remaining percentages being bronze. As is characteristic of bronze, aluminum bronze is corrosion and wear resistant with exceptional strength and toughness.
Manganese Bronze has 55% to 65% copper, 20% to 25% zinc, 1% to 5% manganese, and 1% to 5% iron and has a resistance to corrosion, excellent strength with wear resistance, and extraordinary mechanical properties.
Silicon Bronze is a bronze alloy with 96% bronze and 4% silicon, which makes it easy to machine and cast. It is normally used to produce ball bearings, bearing cages, spacers, gears, and parts of valves.
Brass
Brass is another alloy of copper that contains varying percentages of copper and zinc. The changes in the amount of copper and zinc alters the properties of brass and gives it different characteristics including its appearance. Brass is rust and corrosion resistant due to its zinc and copper content and the absence of iron or iron oxide.
The copper content of brass gives it good conductivity and tensile strength that makes it easy to bend and form. The popularity of brass for molding is its ability to retain its exceptional strength after being formed.
Zinc
Zinc sand casting allows designers to create components with thinner walls, remove draft angles, and insert long narrow holes. To increase its strength, rigidity, castability, and toughness, zinc is alloyed with copper, aluminum, and magnesium. Although it is easier to use in manufacturing than aluminum, zinc is two and half times heavier than aluminum. As with aluminum, zinc has excellent corrosion resistance.
Additionally, zinc has high hardness, which makes it possible to create parts with thin walls. It is used to create complex shapes with tight tolerances that have a long life of usefulness.
Lead
Lead has been sand cast for hundreds of years back to the time of the Romans. It is a heavy metal that is corrosion resistant. The use of lead for sand casting requires a great deal of care due to the health dangers from inhaling it. Many countries have set standards that stipulate the maximum amount of lead that can be used in manufacturing.
Regardless of its negative effects, lead is still used today in sand casting. It is used to produce small to medium parts such as plumbing fittings and decorative objects.
Copper
Copper is normally alloyed with other metals to enhance its mechanical and physical properties. It is stronger than aluminum with high tensile strength but is more expensive and heavier than aluminum. The popularity of copper as a casting material is due to its electrical and thermal conductivity. It does not corrode, which makes it ideal for a wide assortment of products.
As with lead, copper has been used for thousands of years to make several home and industrial products. Sand casting of copper is an inexpensive method for producing copper objects in large quantities, such as plumbing fixtures and hardware.
Ferrous Metals
Iron
Iron in various forms is ideal for casting due to its fluidity, low volume shrinkage, and linear shrinkage. It has poor mechanical properties with compressive strength that is four times higher than its tensile strength. Iron is used for complex shapes, asymmetric structures, and intricate parts.
Gray Iron Castings - Gray Iron has excellent castability and machinability and is known for its low production cost and compressive strength. As with various non-ferrous metals, cast iron has exceptional thermal conductivity and retains its dimensional stability at high temperatures. It is a fragile metal with low impact and tensile strength.
Ductile Iron Castings - Ductile iron has good fluidity with large shrinkage, which makes it susceptible to shrinkage cavities and porosity. Unlike gray casting iron, ductile casting iron has good mechanical properties with abrasion and impact resistance and fatigue strength.
Malleable Iron - Malleable iron is white cast iron that has been annealed, which transforms the brittle structure of white cast iron into a malleable one. As its name indicates, malleable iron has excellent ductility, machinability, toughness and corrosion resistance. Like most iron, malleable iron rusts but is used to produce hand tools, pipe fittings, brackets, and electrical fittings. Aside from its susceptibility to rusting, malleable iron has a poor strength to weight ratio.
Mild Steel
Mild steel is a low carbon steel made from iron, carbon, and other elements. Since it contains 0.15% to 0.30% carbon, it is very malleable and ductile. An increase in the carbon content gives it greater hardness, strength, and hardenability. Mild steel is widely used in sand casting due to its being inexpensive and easy to work. Since mild steel can be machined, forged, and welded, it is used for several types of engineering projects. The difficulties with mild steel include sand inclusions, air holes, cracks, and shinkage.
Stainless Steel
Stainless steel is a popular choice for sand casting due to its exceptional properties, which include resistance to corrosion, durability, and strength. A factor that makes it ideal for sand casting is its low coefficient for thermal expansion, which makes it a good choice for applications that require exceptional accuracy, high tolerance, and dimensional stability.
Although stainless steel is tough and strong, it has a density of 7.8 grams per cubic centimeter and is a lightweight metal for casting essential parts. Unfortunately, stainless steel is an expensive metal due to its chromium and nickel content. Additionally, the high strength and stiffness of stainless steel makes it difficult to eject parts from the sand casting mold.
Alloy Steel
Alloy steel is made by combining carbon steel with cobalt, chromium, manganese, nickel, tungsten, molybdenum, or vanadium. The choice of alloying elements modify and change alloy steel’s strength, hardness, and corrosion resistance. Generally, alloy steel has excellent ductility, wear and shock resistance, strength, and toughness. It is difficult to machine, form, and weld compared to carbon steel.
Several industries use alloy steel to manufacture parts that have to endure significant stress such as automotive parts, structural supports, pipelines, and ship components and structures. The wide use of alloy steel is its cost, which is less than that of stainless steel.
4: Applications and Advantages of Sand Casting
This chapter will discuss the applications and advantages of sand casting.
Applications of Sand casting
The applications of sand casting include:
Pump bodies
Bearings
Bushings
Air compressor pistons
Impellers
Electronic equipment
Engine crankcases
Fittings
Engine oil pans
Gears
Flywheel castings
Gas and oil tanks
Machine parts
Advantages of Sand Casting
As much as sand casting can have disadvantages such as:
Low material strength - When compared to a machined item, the material strength is low because of the excessive porosity.
Low dimensional precision - Dimensional accuracy is particularly poor when shrinking and finishing the surface.
Internal sand mold wall surface roughness results in poor surface finishes.
Flaws are unavoidable - Defects or quality differences, such as shrinkage, porosity, pouring metal defects, and surface defects, are inherent in any metallurgical process. When compared to other casting methods like die casting and investment casting, sand casts have a high level of porosity.
Post-processing — if a tighter tolerance is necessary to interface with other mating parts, a further machining operation is frequently required. In comparison to tooling and material costs, processing costs are significant.
Conclusion
Sand casting is a manufacturing process in which liquid metal is poured into a sand mold, which contains a hollow cavity of the desired shape, and then allowed to solidify. When casting, a liquid material is poured into a mold, which then solidifies to give the desired shape. Casting materials include metal, concrete, epoxy, plaster, and clay. It is essential to select the right method/technique in sand casting, cognizant of the type of sand intended for use.
ZheJiang Dongrun Casting Industry Co,.Ltd was built in 1995, We have been in the casting industry for more than 25 years. No matter what type of molding you need done, we are the right supplier for your jobs. Unlike other of our competition, we offer four types of castings.
Dongrun Casting have 20000 square meters facility houses and 200 production & test equipment, From quotation and tooling design to casting and finished machining, we can work with you at every stage. We serves wide range of industries-from Fortune 500 corporations to small and midsize OEMs. Our products includes:
❖ HVAC | ❖ Architectural parts |
Browse our online showroom to see what we can do for you. And then E-mail:dongrun@dongruncasting.com us your specifications or inquiries today