The Application of Aluminum Castings in the Marine Industry
Aluminum castings have become a cornerstone of innovation and efficiency in the marine industry, offering a blend of strength, lightweight properties, and corrosion resistance that is vital in marine environments. From small recreational boats to large commercial vessels, aluminum cast components play an essential role in ensuring performance, safety, and longevity.
Why Aluminum Castings?
Aluminum is favored in the marine industry for several inherent properties:
Corrosion Resistance: Especially when treated or alloyed correctly, aluminum offers excellent resistance to saltwater corrosion, making it ideal for prolonged exposure to marine environments.
Lightweight: Compared to steel, aluminum is significantly lighter, which helps reduce overall vessel weight and improve fuel efficiency.
High Strength-to-Weight Ratio: It provides the necessary strength without the added mass, crucial for structural and functional parts in ships.
Thermal and Electrical Conductivity: Useful in applications requiring effective heat dissipation or grounding.
Castability: Aluminum can be easily cast into complex shapes, allowing for design flexibility in custom marine components.
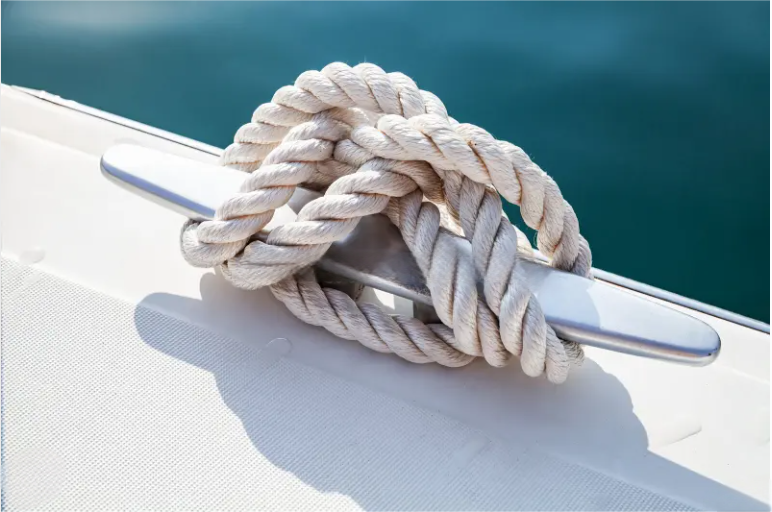
Key Applications in the Marine Industry
1. Engine and Transmission Components
Aluminum castings are commonly used in:
Cylinder heads
Engine blocks
Water pump housings
Transmission casings
These parts benefit from aluminum’s ability to withstand heat, pressure, and corrosion while minimizing weight for performance and efficiency.
2. Propellers and Impellers
Marine-grade aluminum alloys are used to cast propellers and pump impellers due to their durability and resistance to saltwater degradation. These components require precise geometry and high strength, which aluminum castings can deliver.
3. Deck and Hull Fittings
Components such as:
Fairleads
Winch bases
Brackets and reinforcements
These fittings benefit from aluminum’s structural integrity and aesthetic finish. Additionally, they are often anodized or coated for enhanced corrosion protection.
4. Electrical Enclosures and Housings
Electronic and navigational systems need protection from moisture and corrosion. Aluminum cast enclosures are lightweight, heat-conductive, and corrosion-resistant, making them ideal for marine-grade electrical systems.
5. Heat Exchangers and Cooling Systems
Due to aluminum’s high thermal conductivity, castings are commonly used in:
Heat exchangers
Oil coolers
Seawater-cooled engine parts
These parts help maintain optimal engine performance under varying marine conditions.
Common Aluminum Casting Processes Used
Die Casting: Ideal for producing high-volume, dimensionally accurate components.
Sand Casting: Suited for larger or complex geometries and lower volume runs.
Permanent Mold Casting: Offers better mechanical properties and a smoother finish than sand casting.
Challenges and Considerations
Galvanic Corrosion: When aluminum is in contact with more noble metals in seawater, it can corrode. Proper insulation or coatings are necessary.
Surface Protection: Anodizing or applying marine-grade coatings helps prolong service life.
Alloy Selection: Marine-grade aluminum alloys such as 5083 or 535 are commonly used due to their high corrosion resistance and weldability.
Here is a radar chart comparing Aluminum Castings, Stainless Steel, and Composites based on key performance factors for marine applications:
Aluminum Casting scores high in corrosion resistance, lightweight, and castability—ideal for many marine parts.
Stainless Steel offers unmatched strength and corrosion resistance but is heavier and more costly.
Composites are extremely lightweight and cost-effective but have lower castability and strength.
Conclusion
Aluminum castings continue to be a material of choice for marine manufacturers seeking performance, weight savings, and resistance to harsh sea conditions. With the rise of sustainable and efficient vessel design, aluminum’s role in marine applications is poised to grow further, supported by advancements in casting technology and material science.
Dongrun Casting has 20000 square meters of facility houses and 200 production & test equipment, From quotation and tooling design to casting and finished machining, we can work with you at every stage. We serve a wide range of industries-from Fortune 500 corporations to small and midsize OEMs. Our products include Automotive&trucking, Electric Utility & Communications, Metering Systems, the Hydraulic Industry, Medical Devices, Lighting, Fuel and Gas Pressure, and Furniture parts.
More Details: www.dongruncasting.com